Information
Minimize substrate costs - maximize profit: It pays off!
Proven many times, certified and guaranteed optimization of biogas plants through efficient repowering
The company Weber Entec GmbH & Co. KG as a manufacturer of highly efficient ultrasonic disintegration systems in the biogas plant sector is your specialist to make even the most difficult substrates available. The enormous mechanical forces generated by the implosion of cavitation bubbles - the physical principle behind the technology - are used for this purpose.
Ultrasound effect - Versatile:
Ultrasonic treatment has a positive effect at various points within the fermentation process. By breaking down the substrate, the degradation process is accelerated. Furthermore, the flow properties are sustainably improved, which in turn saves pump and agitator power and solves floating layer problems. Both result in the substrate's degradation rate being improved. As a result, the biogas yield is significantly increased, or substrate can be saved or replaced by more difficult or less expensive substrates. Some operators also use the ultrasonic disintegration system to increase the space load of their biogas plant without negative biological consequences and losses in gas quality.
No risk, because success is guaranteed:
Whether grass silage, turkey manure, wheat, corn silage, goat manure, wilted silage, pasture grass or sorghum - Weber Entec ensures optimal degradation! The operator needs less substrates and even gets this guaranteed. Numerous references at home and abroad, independently evaluated and certified, confirm the competence of Weber Entec.
Easy to integrate:
Consulting, planning, manufacturing, installation and commissioning from a single source.
The integration of the ultrasonic disintegration system is done individually and is possible on all types of systems. The operator benefits here from the experience of Weber Entec.
Our technology - your benefit!
With ultrasonic technology from Weber Entec, you are opting for an innovative technology that brings you numerous advantages.
Services
ULTRASONIC DISINTEGRATION SYSTEMS FOR SEWAGE AND BIOGAS PLANTS
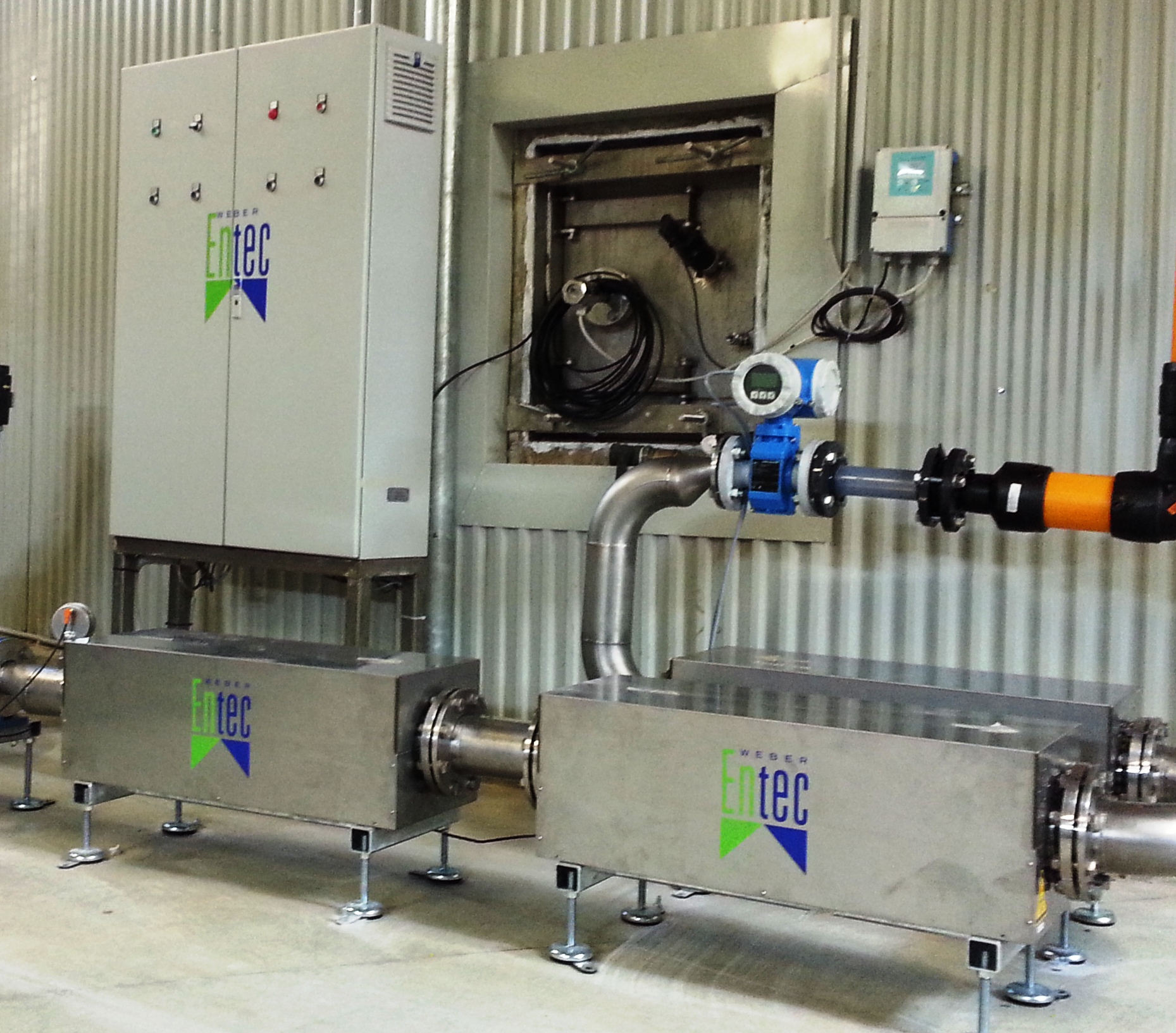
In several years of cooperation with the Fraunhofer Institute IKTS, Weber Ultrasonics has developed a process for sewage sludge disintegration that is superior to the currently available processes in decisive technical aspects and can thus be used more universally and, above all, more cost- and energy-efficiently. The approach of the scientists of the Fraunhofer Institute, proven by years of basic research, as well as the broad-based and long-standing industrial experience of Weber Ultrasonics GmbH finally led to a process which is now available as a market-ready industrial product.
ADVANTAGES FOR WASTEWATER TREATMENT PLANTS:
- Reduction of digested sludge masses to be disposed of by up to 15 % (reduction of disposal costs)
- Increase in biogas yield by up to 25 % (generation of thermal and electrical energy)
- Improved dewatering result by up to 12 % (reduction of disposal costs)
- Reduced polymer consumption by up to 15
- Reduction of digester volume (relevant for new designs or overloaded digesters)
- Destruction and reduction of filamentous microorganisms Improvement of sludge sedimentation in the secondary clarifier
- Minimization of foaming problems in the digester
- Reduction of excess sludge production (relevant for aerobic sludge stabilization, reduction of disposal costs)
- Improvement of denitrification capacity, production of internal hydrogen sources (cost savings by reducing external C sources)
BIOGAS PLANTS:
Ultrasonic technology treats the substrate that has already been fed and mixed in the digester. The ultrasonic disintegration unit treats a partial stream of the pre-fermented substrate from the main fermenter. First, the material is pumped into a macerator, which serves as a stone trap and pre-crushes agglomerates from the fermenter. This prevents clogging of the pump. From there, the liquid enters the ultrasonic units, the Biopush, a clog-free flow cell. The power input of 2,000 watts each ensures cavitation. Extremely high temperatures of up to 5000 °C and very high pressures of up to 1000 bar are generated for a short time, causing high shear forces. Ultrasonic treatment has a positive effect at various points within the fermentation process. Digestion of the substrate accelerates the degradation process, which is additionally supported by the activation of exo-enzymes. Both of these factors lead to an improvement in the degree of degradation of the substrate. As a result, the biogas yield is significantly increased, or substrate can be saved. Furthermore, viscosity is sustainably reduced, which in turn saves pump and agitator power and solves floating layer problems.
ADVANTAGES FOR BIOGAS PLANTS:
- Increase of biogas yield up to 25%
- Increase of degradation rate up to 25%
- Same performance with reduction of substrate feed up to 15%
- Reduction of fermentation time 8 to 15%
- Reduction of own energy demand up to 15%
- Reduction of residual gas potential - Higher substrate efficiency
- Reduction of residence time - Increase of space load
AMPTS II laboratory fermentation with precise online data acquisition
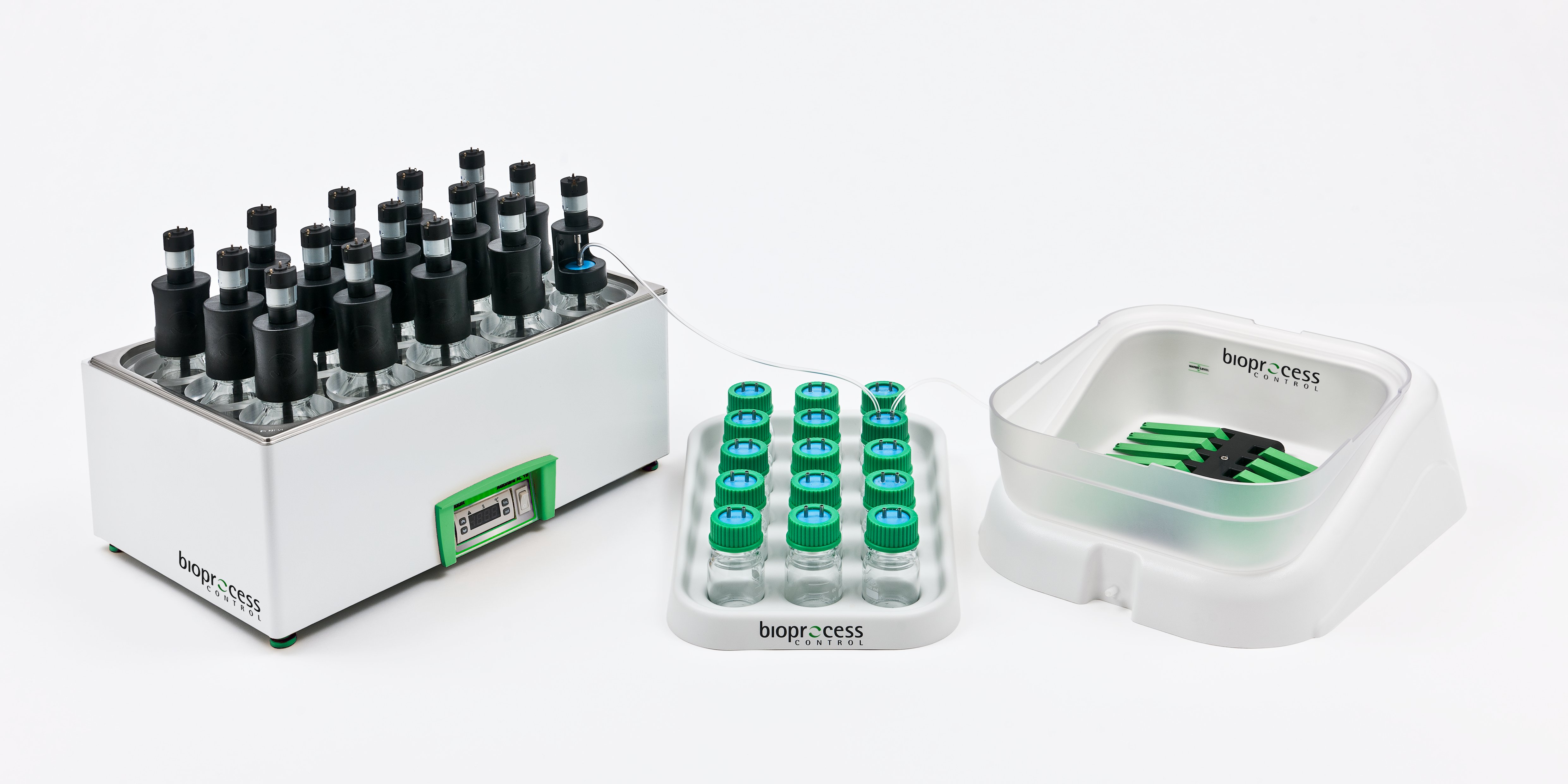
AMPTS stands for Automated Methane Potential Test System. This test unit enables automated recording and evaluation of gas volume flows resulting from the anaerobic degradation of a wide variety of substrates. With little laboratory effort, the gas production and degradation rate can be measured and essential operating parameters such as residence time, type of substrates used, mixing ratio of the substrates and substrate preparation can be evaluated and determined.
The AMPTS II is based on the fundamentals of conventional systems for determining gas potential. The elements of laboratory fermenter and CO2 fixation are supplemented by online volume flow measurement and automated data acquisition and evaluation.
ADVANTAGES:
- Reduced workload and time required due to automated process
- Online recording and real-time evaluation of the entire biomethane production and kinetics
- Integrated pressure +temperature measurement and normalization of the measured values
- User-friendly operator interface for displaying current data
- High data density for determination of process kinetics parameters
- Web-based software via integrated server
- Access and control from any PC, independent of location
- Data available for further processing in standardized form (excel, csv)
- Simple and low maintenance effort
- The current market leading system solution
Projects
BIOGAS PLANT 700kW IN JENA:
In a long-term test on one of two parallel operated biogas plants in Jena (700 kW) in the period from October 2011 to September 2012, Weber Entec proved the efficiency of the plant. The operator of the BGA had asked the "Landesanstalt für Landwirtschaft Thüringen" and the "Thüringer Ministerium für Landwirtschaft, Forsten, Umwelt und Naturschutz" to accompany the test as an independent "expert", so to speak. The company Eurofins was commissioned with the necessary analysis to prove the increase in efficiency on the basis of the relevant parameters. The 14-page final report can be viewed or downloaded at any time from the Weber Entec website. The report details the changes to the substrate feed and takes a holistic view of the influence of the technology on the operation of BGA Jena. The final report certifies an efficiency increase of more than 11% for the plant and net savings of more than 50,000 euros for BGA Jena over the test period - energy self-sufficiency and maintenance already deducted. Following the successful test, the second line has now also been equipped with the ultrasonic technology.
The aforementioned study confirms that the depreciation costs, electricity consumption and maintenance costs for such a system are significantly below the additional yield.
Reference project 2
A similar test was also conducted in Italy and certified by the University of Milan (Politecnico di Milano). Here, a performance increase of 13.4% was measured.
Markets
Contact
Weber Entec GmbH & Co. KG
Weber Entec GmbH & Co. KG
Im Ermlisgrund 10
76337 Waldbronn
Germany
Weber Entec GmbH & Co. KG is responsible for the content of this company profile as well as the compliance with the copyrights of the image material.