Information
ADVANCED AND INNOVATIVE FILTER PRESS TECHNOLOGY
As one of the worldwide leading supplier of mechanical separation technology, MSE Filterpressen GmbH lives from the innovative strength and pioneering spirit of a brand “Made in Germany". With a clear focus on future markets, we develop mechanical filtration plants for the extraction and processing of various sludges, among others from following industries:
- Mining
- Metal
- Alumina
- Energy
- Chemistry
- Pharma
- Food
- Environment and waste water
MSE Filterpressen® offers a wide range of individually tailored filter presses with sidebar technology suitable for both standard and medium duty and for heavy-duty performance levels. Maximum flexibility is provided by choosing between simple manual to fully automated high-tech filter press designs such as the CellTRON®.
For effective dewatering of tailings our equipment is setting state-of-the-art standards offering a technologically and economically outstanding solution. Our constant striving for optimisation and innovation allows our customers to break new ground, discover new possibilities and achieve new successes. We provide solutions, not just machines.
More than 3,000 references underpin the vast experience we have and the trust our customers put in our know-how. We have grown our operations to cover 30 nations globally, and have taken the world lead with our special treatment plants for phosphate filtration in automotive industry.


Services
STRUCTURE OF A FILTER PRESS MACHINE
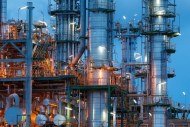
MSE filter presses are designed in modular design. The basis for this is the solid and heavy-duty steel filter press frame, which consists of the following main components: Feeding stands with filtrate outlet (head piece), hydraulic stand with locking cylinder (pressure piece), cross beam and side rails on which the individual filter plates including filter cloths are arranged accordingly. MSE filter presses such as the chamber filter press or the membrane filter press can be configured as required depending on the series. Depending on the respective series, the design of a filter press machine also offers for instance the following automation and expansion options: Automatic plate shifting, vibrating devices for rapid cake discharge, automatic filter cloth cleaning or membrane technology.
MSE filter presses are designed to work with a single hydraulic cylinder. Regardless of the filter press size (including 2000x2000mm), this design results in solid, reliable, and insensitive automation features with lower performance, fewer control valves, and lower complexity than multi-cylinder designs. The sidebar filter press line from MSE is also lighter, cheaper, and handier than an overhead filter press because of its design.
Compared to our domestic and foreign competitors, our systems stand out above all through their longevity and reliability. Our filter presses and features are low-maintenance and highly efficient thanks to the perfect interaction of all components. Upon request, our project-specific filter presses are designed for an operating pressure of up to 30 bar in order to be able to filter even the finest particles. In special cases, a higher design is possible. A structured project management and a professional service is what you can expect from us in any case.
SELECTION OF THE RIGHT FILTER PRESS FOR OPTIMUM SOLID-LIQUID SEPARATION
The number, type and size of the movable plate package is determined by the medium to be filtered and thus determines the format of the filter press machine. MSE filter presses can be used for a variety of applications due to their design specific variability. The size of the solid particles to be separated using special filter cloths extends from the µm range (e.g. enzymes) to the mm range (e.g. sewage sludge). MSE Filterpressen supplies filter plate sizes from 400×400 mm for small (mostly) functional laboratory filter presses for pilot projects up to 2000×2000 mm for large filter presses (e.g. for use in the chemical industry as well as mining).
THE CellTRON® FILTER PRESS
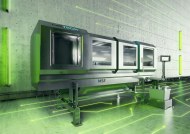
As one of the oldest process filters, the filter press with its high level of automation, efficiency and integration capability forms the solid backbone of mechanical solid/liquid separation. With the introduction of the CellTRON® we are taking a decisive step into the future. The new high-tech filter press, developed primarily for the battery cell manufacturing industry, meets the specific requirements for dewatering special (metal) sludges in the harshest environments.
THE CellTRON® TECHNOLOGY SERIES FOR HIGHEST FILTRATION REQUIREMENTS
The basis of the new filter press line is a fully automatic membrane filter press equipped with special filter plates. True to the philosophy of „reliable“; and „efficient“;, the new product series is equipped with an industry-leading and innovative filter press discharge system with lifetime error message, an automated filter cloth washing system with additionally implemented CIP cleaning function as well as an automatically opening and vacuum-proof machine enclosure with integrated swivelling sluice for defined filter cake discharge.
In contrast to conventional filter presses, this new development guarantees complete, almost gas-tight encapsulation of the filter press to protect the operating personnel and ensure product quality. In addition to standard configurations for applications such as battery cell production, this technology series is also suitable for the most demanding applications that require the highest safety and efficiency standards with highest operational reliability. The CellTRON® product line can treat volatile, dust explosive products as well as substances with toxic and radioactive properties but also PharmaFood products and hot suspensions with filtration temperatures of more than 130°C. With this filter press technology we therefore have a decisive unique selling point.
The CellTRON® product range is available in sizes from 470x470mm to 2000x2000mm with filter areas from 1 m2 to 1. 300 m2. You can choose between the configuration „Light“ for high product and safety requirements and the configuration „Xtreme“ for highest product and safety requirements. The material used for the „Xtreme“ version is almost exclusively stainless steel. Assemblies in contact with the product are designed according to hygienic design criteria in order to prevent product sticking and contamination. Each filter press unit can be supplied as a complete unit with piping, valves, instruments, pumps and tanks.
LIFE CYCLE COSTS OF THE CELLTRON® FILTER PRESS SERIES
Today, the limit for the use of a highly automated filter press (not only for use in battery cell production) is mostly determined by the economic efficiency. The purchase price for a filter press is often the primary purchase criterion. However, it does not always play a decisive role in life cycle costs. Costs for wear parts and maintenance make up a large part of the total costs. Here it is particularly important to realize a robust and solid construction with little filigree and thus susceptible individual parts.
The CellTRON® filter press formats CT4 to CT20 are absolutely standardized. This enables further cost optimization as well as efficient production and, if necessary, rapid repair. After all, the higher investment costs compared to a conventional filter press should pay for themselves relatively quickly due to the elimination of the operators and the increased production. Cost-intensive revisions of the sophisticated design, which are necessary after a short operating time for a large part of the commercial fully automatic filter presses, had to be stopped urgently. In view of the high demand from customers for an autonomous plant for the production of lithium-ion battery systems, MSE Filterpressen has set itself the task of developing an innovative and customer-oriented long-term solution with the new CellTRON® and of reducing maintenance costs to a minimum through solid mechanical engineering. In addition, the special enclosure means that costs can be further minimized by eliminating the need for complex and expensive steel structures and exhaust air systems for buildings and rooms.
CHAMBER FILTER PRESS
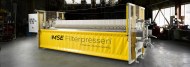
In addition to its simple and inexpensive design, the chamber filter press is also a powerful and reliable filter press. The type of suspension to be filtered (e.g. mining, chemical or pharmaceutical industry) is irrelevant. In order to meet the different requirements of industry and municipalities, MSE chamber filter presses are designed for this in modular design. The solid and heavy-duty steel filter press frame, which consists of the following main components, forms the basis: Feeding stands with filtrate outlet (head piece), hydraulic stands with locking cylinder (pressure piece), cross beam and side rails on which the individual filter plates are arranged accordingly including filter cloths. The plate pack also consists of uniform chamber plates with a cut-out of 15-50 mm for holding the puncture-proof filter cake. Polypropylene (PP) is used as the chamber plate material in the standard version.
HIGH PERFORMANCE AND HIGH DEGREE OF CONFIGURATION FOR YOUR CHAMBER FILTER PRESS
The chamber filter press can be configured as required depending on the series. These include, for example, automatic plate shifting, a vibrating device or core blow-out and/or core rinsing. Taking different influencing factors into account, chamber filter presses achieve a solids content in the filter cake from 30 to over 50 percent. The intelligent filtration principle leads to immense cost savings in the waste water sector, for example. The operation of the chamber filter press is designed for a feed pressure of up to 30 bar in order to successfully filter even the finest particles.
FILTRATION PRINCIPLE
At the beginning of the filtration cycle, the press and the filter plates are closed by a (hydraulic) locking cylinder. The closing cylinder presses the filter plates against each other via the pressure plate and increases the hydraulic pressure accordingly up to the required nominal closing pressure. Due to the design, a chamber is formed between the individual filter plates, which represents the process chamber. The suspension to be filtered is pumped into the chambers with a suitable feed pump through the turbidity inlet at the feed stand and concentrated there. Depending on the respective application, the filter plates are lined with special filter cloths which visibly retain the solids during the flow, taking into account the process characteristics.
DISCHARGE OF THE FILTRATE / EMPTYING OF THE CHAMBERS
The filtered and clear liquid (filtrate) is discharged along a channel system (open filtrate outlet) into the laterally mounted filtrate channel. A closed filtrate outlet is also available as an option. The solid material, on the other hand, remains in the plate chamber as a solid filter cake. The increasing feed pressure compresses and dewaters the resulting filter cake in the chamber. Once the throughput has fallen to a predetermined minimum, the pressure has increased significantly and the individual chambers inside the filter plates are completely filled with the filter cake, the filtration process is complete. To empty the chambers, the closing pressure of the filter press is released, the filter press is opened and the cake is removed from the filter cloths. The filtration cycle is then repeated.
Markets
Contact
MSE Filterpressen GmbH
MSE Filterpressen GmbH
Am Eisengraben 3
75196 Remchingen
Germany
MSE Filterpressen GmbH is responsible for the content of this company profile as well as the compliance with the copyrights of the image material.