Information
Improved energy efficiency not only reduces CO2 emissions and relieves the environment, but also lowers operating costs. For us, increased energy efficiency also involves reducing risks and achieving security of supply. Because it is only through the interaction of all parameters that we achieve sustainable solutions for our customers.
We deliver energy tailor-made suits, plant optimization, planning, construction and operation of infrastructure plants and cross-sectional technologies. Savings contracting and energy supply contracting.
In doing so, we have further developed classic contracting. For us, it is not enough to offer customized contracting solutions. We enter into energy-saving partnerships with our customers and allow ourselves to be measured by our results: Because we guarantee savings contractually. In addition, we naturally also offer contract models for pure media supply or as part of full-service models.
We proactively develop solutions for improved energy efficiency for our customers and implement them - because we are aware of our social and ecological responsibility.
Services
Performance specification 1
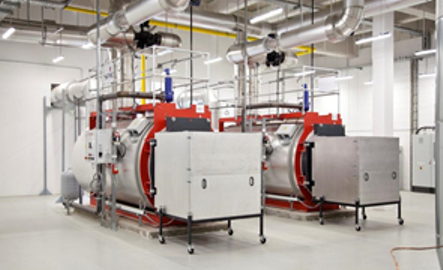
EFFICIENT ENERGY SOLUTIONS
Improved energy efficiency not only reduces CO2 emissions and helps the environment, but also lowers operating costs. For us, increased energy efficiency also involves reducing risks and achieving security of supply. Because it is only through the interplay of all parameters that we achieve sustainable solutions for our customers.
In doing so, we have further developed classic contracting. For us, it is not enough to offer tailored contracting solutions.
We enter into energy-saving partnerships with our customers and allow ourselves to be measured by our results: Because we guarantee savings contractually.
In addition, we naturally also offer contract models for pure media supply or as part of full-service models.
In order to protect the climate and support the energy transition, we are also active in the field of electromobility.
We proactively develop solutions for improved energy efficiency for our customers and implement them - because we are aware of our social and ecological responsibility.
We are active in the following areas:
ENERGY MANAGEMENT
ENERGY INFRASTRUCTURES
MEDIA SUPPLY AND ENERGY DELIVERY
ENERGY EFFICIENT LIGHTING
CONSULTING
Projects
TAKEDA PHARMA, Singen - Energy Performance Contracting
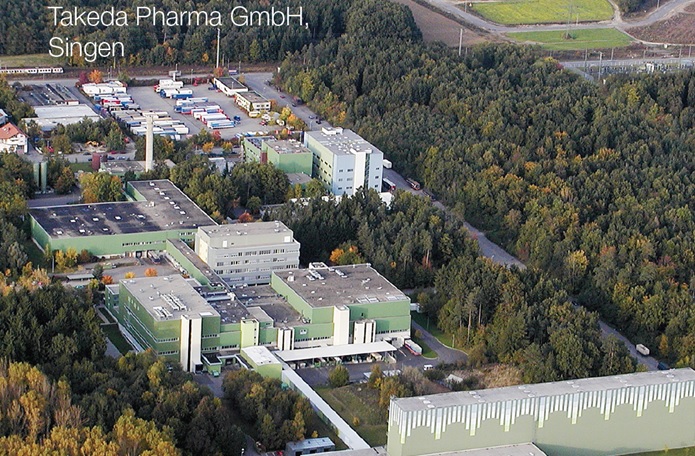
Takeda Pharma GmbH in Singen is part of the globally active group of Takeda Pharmaceutical Company Ltd. With around 600 employees, Singen is one of the large sites with the business units Production and Administration.
At the Singen plant, Takeda manufactures drugs in various dosage forms. The main focus is the production of the drug Pantoprazole as a freeze-dried powder, which is filled into small glass vials. These very durable vials are then filled with a solution and administered intravenously to the patient during treatment in the clinic or doctor's office on site.
In addition, Takeda in Singen produces a nasal spray for hay fever allergy sufferers as well as various ointments and suppositories.
For this site, SPIE Energy Solutions GmbH was commissioned to holistically analyze the energy infrastructure for possible cost and CO2 savings. The result of this analysis was a package of measures individually tailored to Takeda's needs, with which enormous savings potential could be tapped. Convinced by the results and the approach, Takeda commissioned the energy service provider SPIE to implement the new energy supply concept.
Requirements
The pharmaceutical industry is increasingly confronted with regulatory requirements as well as new demands on development and manufacturing spaces. The implementation of these regulations in a pharmaceutical plant requires high investments with increasing cost pressure.
The goal and aspiration of the project partners was to combine resource and energy efficiency with economic success. Takeda attached importance to a holistic view of the energy infrastructure. The necessary investment costs were to be fully refinanced from the savings.
It was particularly important to Takeda that the implementation should be as interface-free as possible without affecting production, and that both the investment costs and the savings could be planned.
Results
With the implemented energy supply concept, Takeda will save at least 1.1 million euros and about 4,350 tons of CO2 annually in the future. At the heart of the optimization is a combined heat, power and cooling system (CHP) for the combined generation of electricity, heat, steam and cooling. In the future, Takeda will produce around 50% of the electricity required at the site itself. In summer, the heat from the combined heat and power plant (CHP) is converted into cooling using an absorption chiller, thus helping to cool the clean rooms. In addition, a new refrigeration center with two highly efficient chillers was built. Three new cooling towers ensure sufficient chilled water at all times.
Another component of the package of measures is the conversion of parts of the lighting to energy-saving LED technology.
The package of measures is rounded off by a new building control system and an intelligent energy data acquisition system.
As general contractor, SPIE took over the conception, planning and turnkey implementation of the new energy supply concept at a fixed all-inclusive price.
As part of the operational management, SPIE guarantees the achievement of savings over the ten-year contract period.
Services provided by SPIE Energy Solutions
- Design, planning and implementation of a new energy supply concept
- Construction of a CHP plant for the combined generation of electricity, heat, steam and refrigeration
- Securing the projected cost reduction of over 1.1 million euros annually through a savings guarantee
- Energy management (energy monitoring and controlling)
- Maintenance and repair
Individual measures
- Installation of a combined heat, power, steam and cooling plant for the production of electricity, heat, steam and chilled water
- Installation of a CHP heating water route and hydraulic balancing of the heating water network to reduce the heating return or CHP inlet temperatures
- Installation of an air preheater for the steam boiler
- Installation of a new refrigeration unit
- Implementation of an energy-saving LED lighting concept with 600 LED lamps
- Installation of a building automation system
- Introduction of an M-Bus meter concept for energy monitoring
Media: heating, cooling, electricity, light, steam
Contract term: 10 years
Customer benefits
- Reduction of total energy costs of 1.1 million euros net per year
- Guaranteed savings over the contract term
- Assumption of maintenance costs
- Minimized risks, greater security of supply
Awarded the Contracting Award 2014
BENECKE-KALIKO, Eislingen - Energy supply contracting
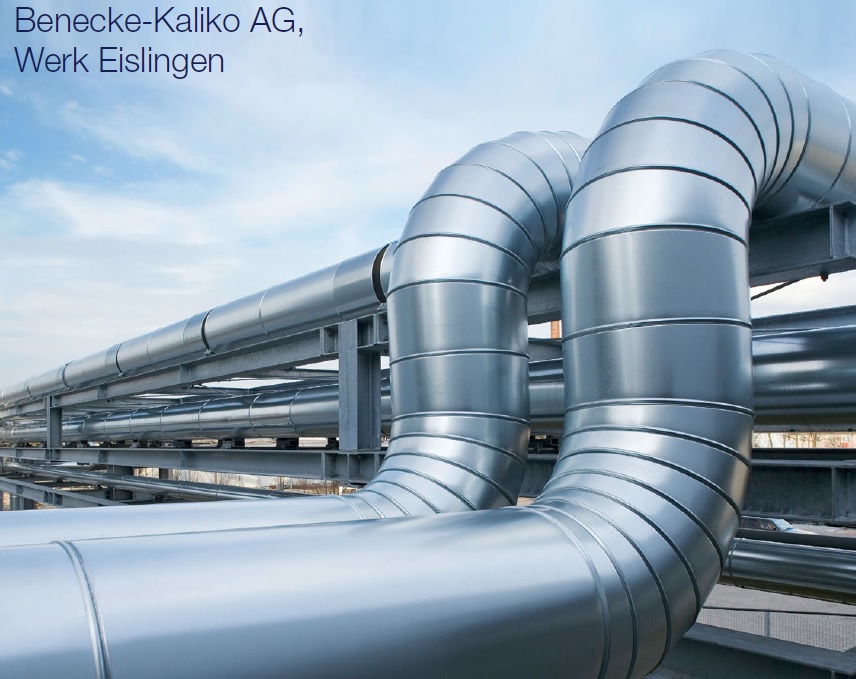
Benecke-Kaliko AG is a company in the Continental AG group of companies. At the Eislingen plant, around 350 employees produce 133 km of film webs every day, mainly for the automotive and automotive supplier industries. Customers mainly use the films for decorative surface coating. Benecke-Kaliko AG produces patented films under its own brand name.
SPIE Energy Solutions supplies the plant with media and ensures a significant reduction in operating and energy costs.
Requirements
At its Eislingen site, the company, which is part of Continental AG's ContiTech group, produces high-quality technical and decorative surfaces for the automotive industry. The plant management was looking for a way to reduce the costs of energy-intensive production and increase capacities for core tasks. Energy management was therefore completely outsourced to a contractor.
SPIE Energy Solutions guaranteed cost reductions in energy and media supply as well as higher supply security and availability.
Results
The plant procures process and heating energy, cooling water and compressed air from SPIE Energy Solutions and commissions them to clean exhaust air containing solvents. Immediate optimization of the existing equipment resulted in a five percent reduction in consumption after only a short time.
Subsequently, SPIE Energy Solutions engineers implemented a new energy supply concept. This included the construction of a new energy center. This houses both the new boiler house for steam generation and the new refrigeration center for the plant's cooling water supply.
In addition, the existing exhaust air purification system was replaced by a modern regenerative thermal oxidation (RTO) system. This achieves significantly better emission values and at the same time significantly lower operating costs. Some of the plant supply piping was renewed. Benecke-Kaliko's investment totaled over 5 million euros.
The eight Benecke-Kaliko employees who were previously responsible for energy technology are now employed by SPIE. The measures resulted in a significant and sustainable reduction in operating and energy costs in media supply, and the contract term is ten years.
Services provided by SPIE Energy Solutions
- Plant refurbishment and new construction
- Plant operation, individual measures
- Construction of a new energy center for the supply of cooling water, steam and compressed air
- Replacement of the existing exhaust air purification plant by a new RTO plant for the purification of solvent-containing exhaust air from the production process
- New construction of a water treatment plant for obtaining cooling water and boiler feed water from river water
- Installation of a control system for all technical supply trades
- Investment in plant refurbishment
- Implementation of various measures to reduce the customer's useful steam consumption
Media
Heat, cooling, water, compressed air
Investments: 5.3 million euros,
Contract period: 10 years
Savings: 24 percent savings in CO2 (equivalent to 3 796 200 kg CO2 /a)
- 48 percent savings in solvent emissions (equivalent to 4,045 kg C ges/a)
- Significant and sustainable reduction in operating and energy costs in the media supply system
Customer benefits
- Lower energy costs
- Reduced emissions
- Greater supply reliability
- Higher availability
- ISO 9001, 14001 and EMAS certifications lead to clearly structured processes and maximum safety
Villeroy & Boch AG, Mettlach - General contractor performance with guaranteed success
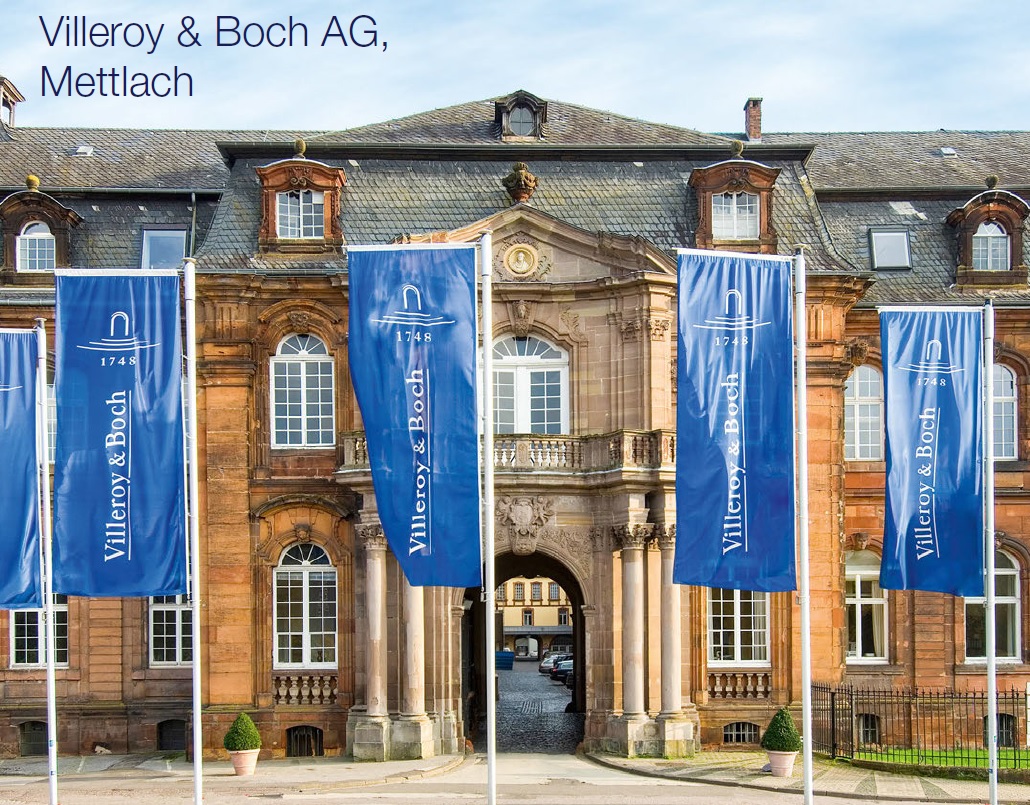
The German group Villeroy & Boch operates worldwide as one of the leading ceramic producers in the areas of bathrooms, wellness and tableware-with 7,400 employees, 14 production sites and subsidiaries in 125 countries. Founded in 1748, the company today stands for excellent design, innovative technology and uncompromising sustainability.
The Group's headquarters is the Old Abbey in Mettlach, Saarland, which was purchased in 1809 by the then owner Jean-Francoise Boch. In 1956, the Mettlach sanitaryware factory was built and modernized and expanded in 1967. Today, washbasins and WCs are manufactured in this automated factory, primarily using the highly efficient die-casting process.
With its sanitaryware factory, Villeroy & Boch sets international standards in terms of environmental management: in 2009, the production facility qualified for the globally applicable ISO 14001 certification and at the same time it was validated in accordance with the EMAS regulation. this was followed in 2014 by ISO 50001 certification for the exemplary energy management system.
Thanks to the support of SPIE Energy Solutions GmbH, Villeroy & Boch was already able to significantly reduce energy consumption at the sanitaryware factory in 2014 and make production much more sustainable.
Requirements
Large ceramic parts, such as a washbasin, must undergo an energy-intensive process during production. In the past, the heat required for this was supplied by steam as an energy source. In the meantime, production technology has developed to the extent that the casting process has been changed from conventional plaster casting to the automated die casting process. Drying now takes place only in gas-fired dryers. This naturally has an impact on the energy infrastructure of production.
This was also the case at Villeroy & Boch. Following the modernization of the production process at the Mettlach sanitaryware factory, the steam supply was to be converted to more efficient energy generation.
Together with the energy experts from SPIE Energy Solutions, a concept was developed to supply the factory with heat and electricity in a particularly effi cient manner, both economically and ecologically.
Results
The measures developed by SPIE were installed in 2013 and 2014. The existing steam supply was replaced by a highly effi cient energy center. This consists of a combined heat and power plant (CHP) with a capacity of two MWel and a boiler plant with a capacity of two times 3.5 MW.
The CHP unit runs on natural gas and generates heat and electricity in a highly efficient manner. The generated electrical energy is completely consumed in the sanitary factory.
To distribute the pumped hot water, SPIE Energy Solutions GmbH built a local heating network more than two kilometers long on the Villeroy & Boch factory premises. The result is impressive: The company's energy costs will be reduced by an amount in the high six-figure range in the future. This corresponds to a saving of around 25 percent, based on the original costs.
At the same time, the energy service provider SPIE Energy Solutions is reducing Villeroy & Boch's CO2 emissions by more than 4,000 tons per year. An efficient step for environmental protection.
For a contract period of 10 years, SPIE will take over operation of the plants, regular maintenance and repairs.
Services provided by SPIE Energy Solutions
- Plant optimization
- New plant construction
- Savings guarantee
Individual measures
- New construction of an energy center
- Construction of a CHP with a capacity of 2 MWel
- Conversion from steam to pumped hot water
- Renewal of the boiler plant to 2 x 3.5 MW
- Installation of a local heating network (2 km)
- Operation, maintenance, repair
Media
Heat, domestic hot water, electricity
Contract term: 10 years
Customer benefits
- Increased process reliability through renewal of heat supply
- Own power generation with the CHP
- Reduction of total energy costs by approx. 25
- Reduction of environmentally harmful CO2 emissions by approx. 4,000 t/a
- Guaranteed savings over the term of the contract
Markets
Contact
SPIE Energy Solutions GmbH
SPIE Energy Solutions GmbH
Flachter Str. 30
70499 Stuttgart
Germany
SPIE Energy Solutions GmbH is responsible for the content of this company profile as well as the compliance with the copyrights of the image material.