Information
As established lightweight construction experts, we develop optimal processes and sustainable solutions for our customers: from product development and machines to the finished part in component manufacturing. Around 700 employees are already working with our customers today on the challenges of tomorrow. And they do so worldwide at our seven locations in Germany, Switzerland, the USA, China and Slovakia.
Holistic competence in the industry through Make & Buy - Felss supplies individual solutions for in-house production or the purchase of components. Here, Felss Systems stands for Make, i.e. mechanical engineering, including prototyping and engineering as well as their sophisticated development and implementation. Felss Rotaform stands for Buy and thus for the entire spectrum of component manufacturing with a global, energy-saving footprint, even in large-scale production.
Since May 2019, the traditional company HMP has been a part of the Felss Group of Companies, headquartered in Königsbach-Stein. HMP is considered a specialist in rolling technology and thus adds another technology to the Felss Group's range of services. The rolling technology is firmly integrated in the Felss group of companies and appears under the brand name HMP ROLLING.
Our claim is to convince customers from different industries with resource-efficient, highly resilient and precise products. Whether for the automotive industry, medical technology, aviation or precision mechanics: Felss is a strong partner in the processing of metallic materials such as steel, aluminum or titanium along the entire process chain. From the blank to the ready-to-install workpiece.
The right process for every requirement
With our know-how in cold forming and many years of experience in building machines for tube processing, Felss offers the right technologies, processes and solutions for all complexities.

Services
Rotary swaging
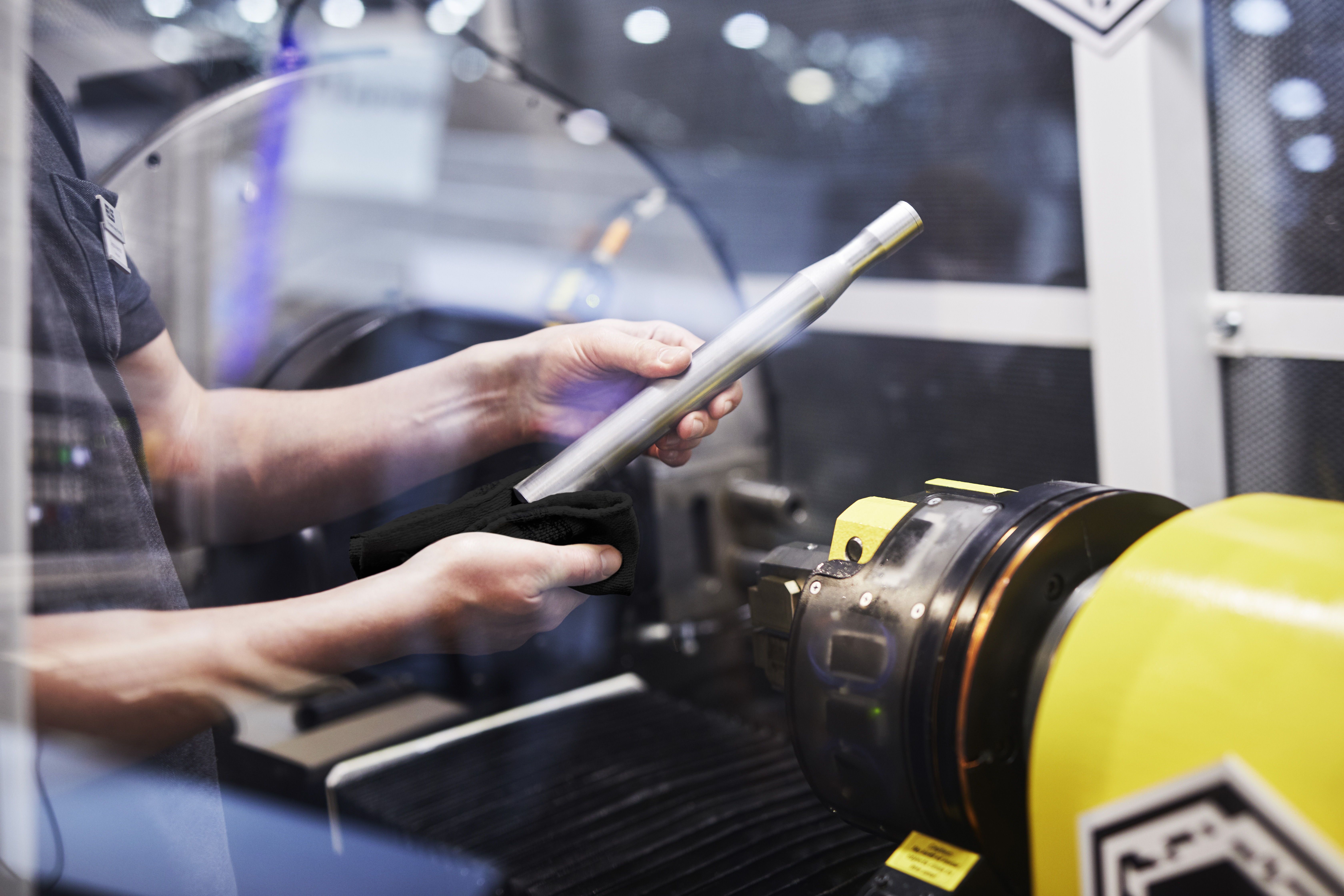
The cold forming process rotary swaging enables efficient and economical production of lightweight components. In this process, several tool segments act simultaneously on a workpiece in rapid succession. The material to be machined begins to flow and is formed with high precision. The process is suitable for forming a wide variety of external and internal geometries. It offers a much wider range of possibilities than most other cold forming processes. For example, a hose connection is just as possible with it as the high-precision and fast production of steering spindles, drive shafts, airbag cylinders or actuators.
Axial forms
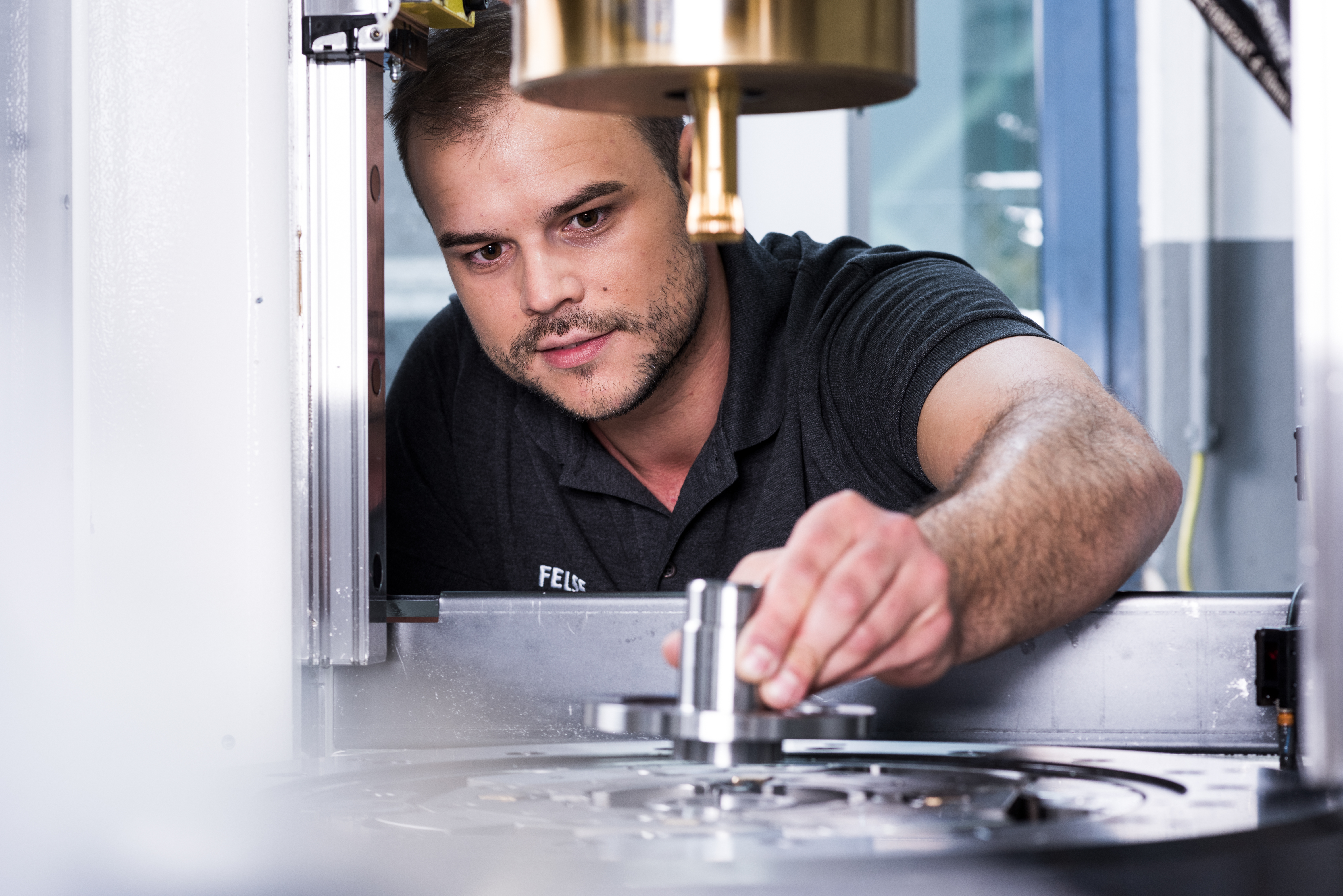
Axial forming offers advantages in many different areas of application, especially for high-quality gear components that require economical production processes. With axial forming, all gear dimensions are achieved with the highest precision. Since the gearing is an exact copy of the tool, there are basically no pitch errors. The profiles are highly precise and the root radius is completely symmetrical, which significantly increases fatigue strength. Each component is produced in short process times and, unlike machining processes, the strength of the components is increased.
Tube+
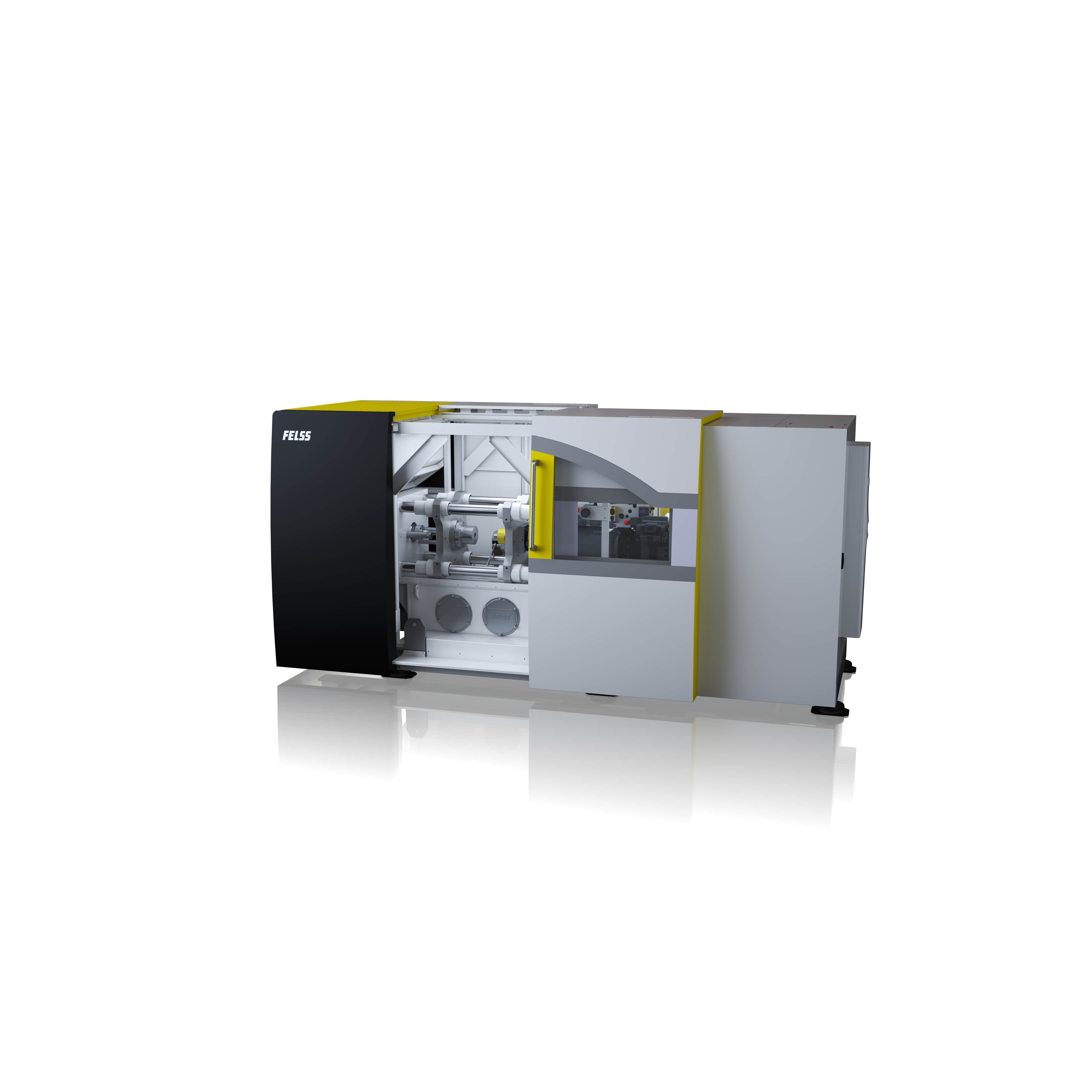
The Tube+ process developed and patented by Felss enables partial tube thickening in the cold forming process for the first time. The process is used in the production of precursors that contribute to simplifying the process chain in subsequent steps. It represents a supplement or alternative to rotary swaging.
HMP Rolling
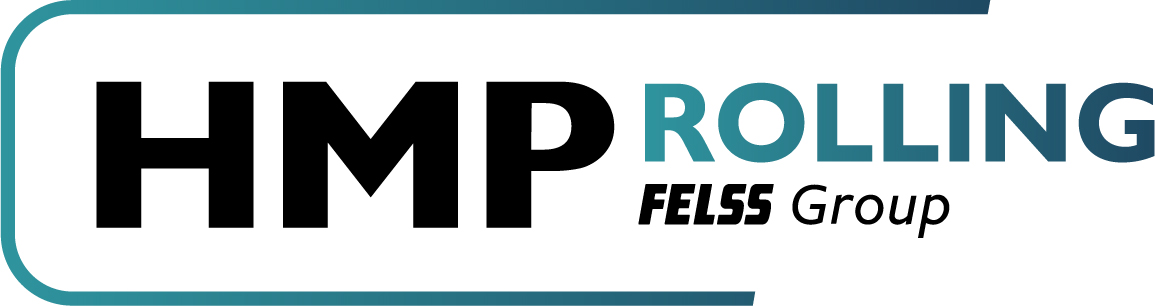
Since the acquisition of the HMP companies in 2019, the Felss product portfolio also includes rolling technologies and equipment of various kinds. Whether wire reducing rolls, flat and profile wire rolls, ultra precision rolls, strip rolls or cross profile rolls.
Projects
Generation e
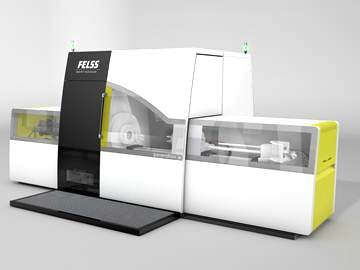
Generation e - a new dimension of flexibility
Be it through batch size adaptability at short notice, long-term expandability of production lines or consistently simple process control: generation e expands the playing field for the numerous utilization advantages of cold forming, thus enabling not only more efficient production processes but also economical component designs in completely new application areas.
E for energy efficient:
Produce sustainably - reduce your energy and raw material consumption. With Generation e, your production is 25% more energy-efficient: the new design not only saves you electricity costs during production, but also operating materials such as lubricating oil - without compromising on production quality. And that's good news not only for your wallet, but also for the environment.
Electric axes: Lower power consumption thanks to intelligent energy management and elimination of hydraulic reactive power.
Stand By: Elimination of energy consumption during downtimes thanks to energy-saving mode.
Lubrication on demand: Targeted lubricant application for lower oil consumption and more cleanliness.
Rotor shaft for hybrid vehicles
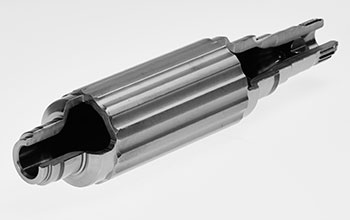
The rotor shaft is produced by a newly developed production process that intelligently links rotary swaging, axial forming and heat treatment. This process allows the hybrid shaft to be realized hollow and with a much simpler plug-in spline.
Component weight reduced
Producing the rotor shaft from tube using the rotary swaging process is not only highly accurate and fast. It also significantly reduces the weight of the component. Weight is an important factor, particularly for electric cars, because every kilogram less increases the range of the vehicles with their relatively heavy batteries. The newly developed production process, in which rotary swaging, axial forming and machining processes are intelligently combined, offers great opportunities for Felss Rotaform in the future .
Markets
Contact
Felss Group GmbH
Felss Group GmbH
Dieselstr. 2
75203 Königsbach-Stein
Germany
Felss Group GmbH is responsible for the content of this company profile as well as the compliance with the copyrights of the image material.